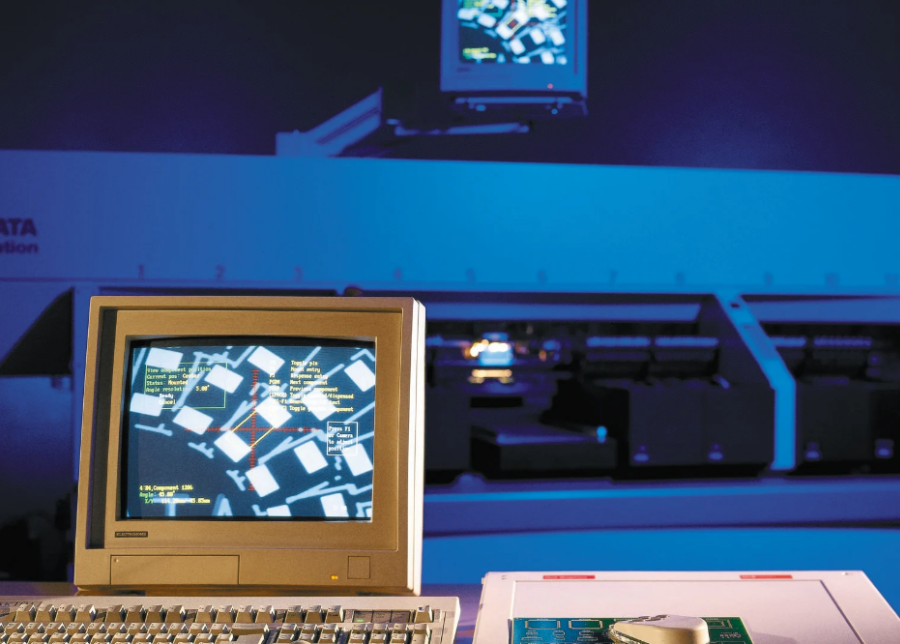
Simplificando la fabricación de alta mezcla durante más de 50 años
Si hay una constante en el ensamblaje de PCB, es el cambio en sí mismo. Ya sea que se trate de combinaciones de productos, componentes o flujos de materiales que cambian rápidamente, los clientes de Mycronic han liderado el camino, controlando la complejidad durante más de 50 años.
Nace un cambio tecnológico
Hasta principios de los años 1980, los componentes con orificios pasantes eran el estándar en la fabricación de PCB. Pero a medida que aumentó la demanda de dispositivos electrónicos más pequeños y compactos, las tecnologías de montaje superficial crearon nuevas oportunidades para una mayor densidad de componentes y un mejor rendimiento.
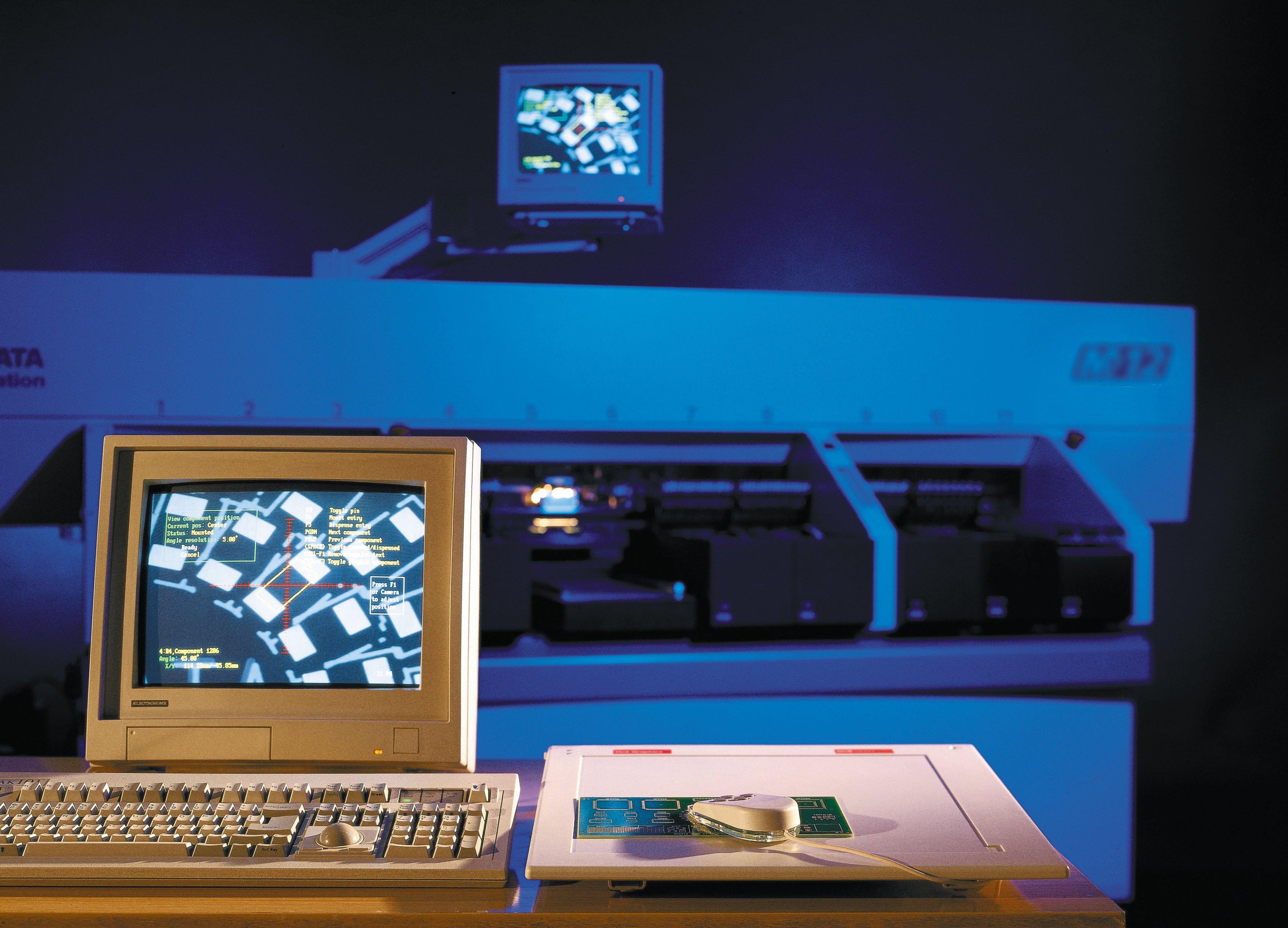
Una pequeña empresa sueca llenó ese vacío. Sus primeros sistemas, que aplicaban un haz de luz que se movía rápidamente para indicar al operador dónde montar los componentes, permitieron a los fabricantes avanzados ensamblar manualmente placas de circuitos con mayor precisión y flexibilidad. Sería el punto de partida de una larga serie de innovaciones que marcarían la industria, desde sistemas flexibles de pick and place y la impresión por inyección de pasta de soldadura hasta líneas de producción totalmente automatizadas.
El ensamblaje ágil en su forma más compleja
“La transición del sistema de orificio pasante al de montaje superficial nos abrió las puertas al principio”, afirma Robert Helleday, director de investigación y desarrollo de Mycronic. “Por supuesto, no estábamos solos, pero nuestro enfoque era único. Mientras que la mayoría de nuestros competidores surgían de la producción interna de las grandes empresas, nosotros veníamos del campo de la producción a pequeña escala y todo lo que hacíamos estaba centrado en estos clientes. Eran productores de series cortas que construían ordenadores avanzados. Eran los grandes desarrolladores aeroespaciales franceses y estadounidenses. En la mayoría de los casos, su producción era extremadamente avanzada y sus componentes eran muy caros”.
Estos productores dependían en gran medida de ciclos rápidos de creación de prototipos y conjuntos complejos de alta densidad. A medida que evolucionaban las tecnologías de pick-and-place de Mycronic, los cambios rápidos y los potentes sistemas de control de procesos eran esenciales. «Crecimos más o menos junto con estos clientes», dice Robert. «Por eso, a medida que nuestras soluciones se volvían más rápidas, más automatizadas y basadas en software, nos mantuvimos en sintonía con sus necesidades diarias».
Cambiando el juego
Para los fabricantes de gran variedad de productos a finales de los años 90 y principios de los 2000, el coste y la complejidad de los cambios de trabajo eran una importante barrera para la rentabilidad. La mayoría de los alimentadores de componentes del mercado eran pesados, voluminosos y requerían un mantenimiento regular. Sus posiciones de alimentación eran fijas y la mayoría requería bobinas de componentes completas, lo que generaba un desperdicio significativo de tiras de componentes sin utilizar.
Pensamiento justo a tiempo
La solución de Mycronic fue el sistema de alimentación Agilis™: un concepto de alimentación compacto, intercambiable y sin mantenimiento. Representaba lo mejor de la filosofía de Mycronic y establecía un nuevo estándar para la preparación y carga rápida y flexible de kits. “Este principio es realmente fundamental en todo lo que hacemos”, afirma Robert, explicando cómo los “flujos de material bidireccionales” impregnaron todas las innovaciones de la empresa en manipulación de materiales y almacenamiento automatizado.
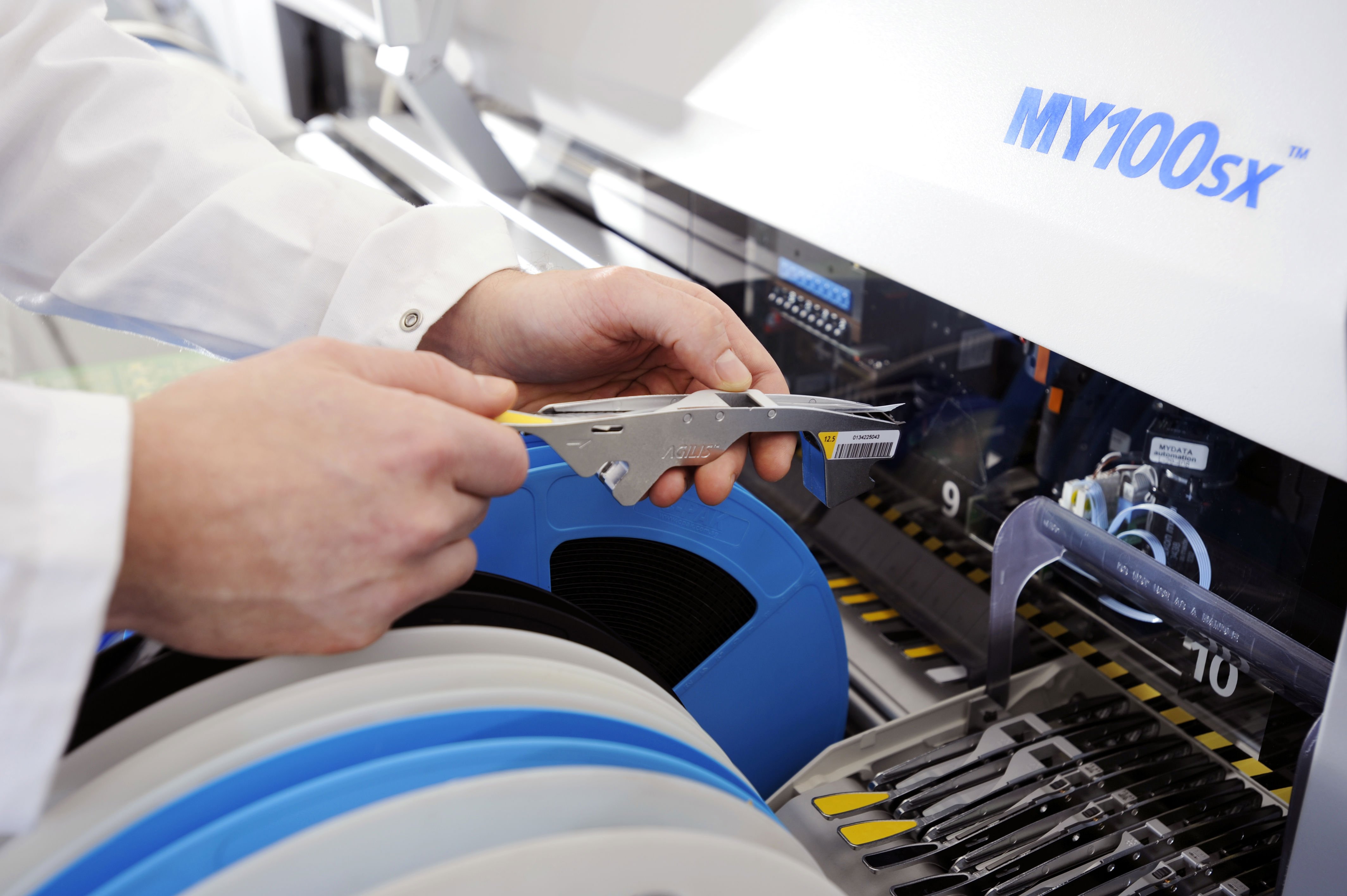
“No se puede seguir alimentando las máquinas porque no siempre se agota todo el rollo”, explica. “Se introducen y se sacan cosas del almacén y la sincronización, el seguimiento y el rastreo de todos estos flujos contribuyen enormemente a una fabricación rentable y ágil. Es un flujo de trabajo integrado que resulta crucial para la producción justo a tiempo. Hay que poder recuperar el material y colocarlo en una placa o en el almacén con la menor intervención humana posible”.
El sistema de alimentación Agilis fue un éxito instantáneo y se convirtió en un símbolo de marca registrada del ensamblaje ágil. Con el tiempo, otros pasos del proceso pasarían por el mismo replanteamiento fundamental. Y la impresión con pasta de soldadura era una de esas aplicaciones que estaba madura para la innovación. «Es una historia interesante», dice Robert, «y una vez más, fue totalmente impulsada por las demandas de los clientes».
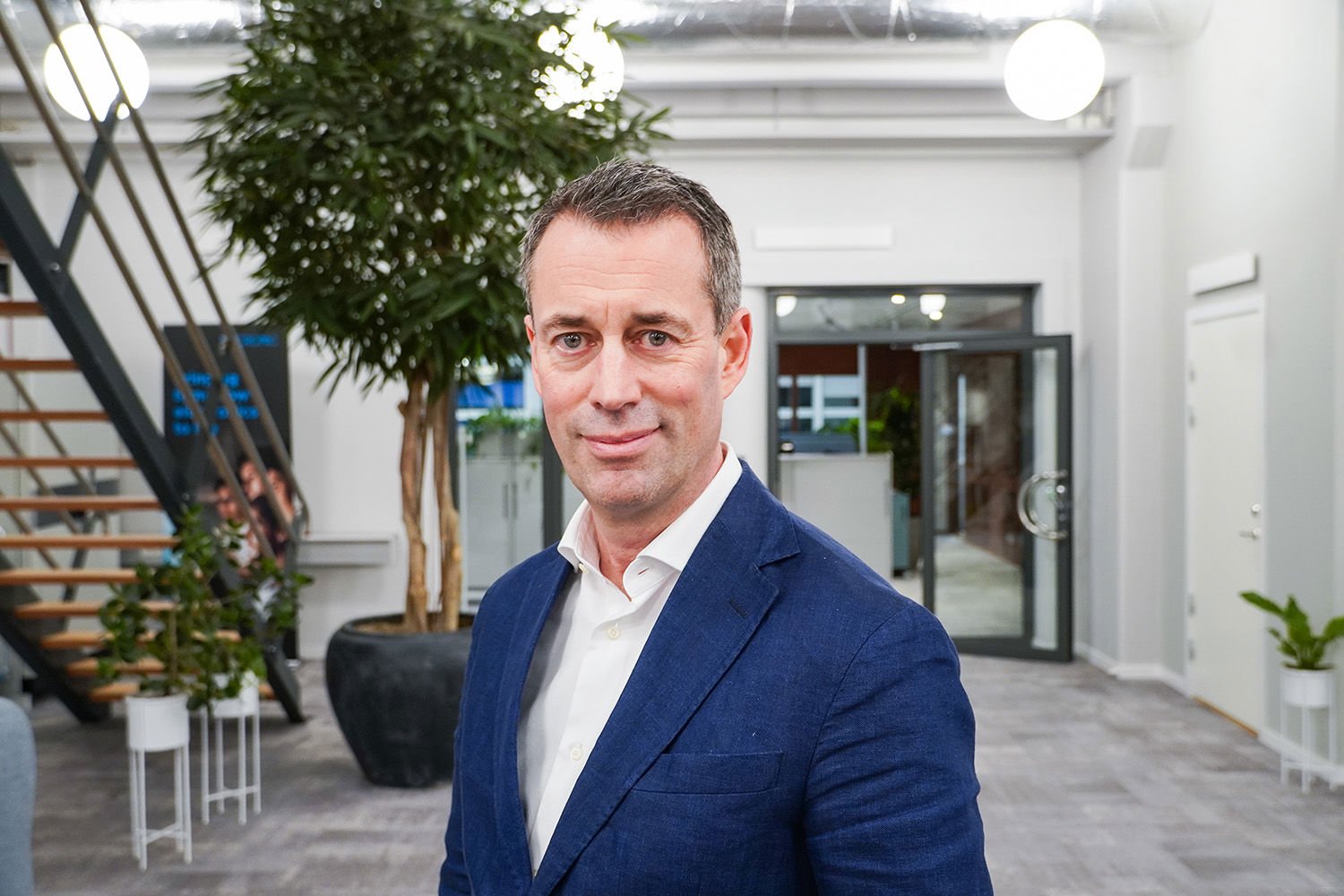
¿Cómo pasar de una escobilla de goma que se desplaza sobre una lámina de metal a un sistema de inyección de alta velocidad totalmente controlado por software con una precisión de nanolitros?Robert Helleday, director de investigación y desarrollo de Mycronic
Impresión de precisión a velocidad de chorro
La idea de la impresión por inyección de pasta de soldadura surgió cuando un antiguo cliente francés se acercó a Mycronic con una tarea aparentemente insuperable. “Nos dijeron: ‘Siempre hemos tenido esta gran máquina de pick and place, pero sería increíble si mi impresión pudiera ser tan flexible’”, dice Robert. “El problema es que todos pensaron que sería imposible. Es decir, ¿cómo se pasa de una escobilla de goma que se desliza sobre una hoja de metal a un sistema de inyección de alta velocidad, totalmente controlado por software y con una precisión de nanolitros? Hizo falta una verdadera iniciativa de I+D a largo plazo, pero logramos crear la primera impresora de inyección. Incluso ahora, 20 años y varias generaciones de máquinas después, nadie ha surgido con una tecnología que sea siquiera similar”.
Siempre hemos sido un poco desafiantes: cuando alguien nos dice que es imposible, eso simplemente nos empuja a pensar en grande.Bobbi Ferm, ingeniero jefe y arquitecto de sistemas de Mycronic
Desafiando las convenciones
Según Bobbi Ferm, ingeniero jefe y arquitecto de sistemas de Mycronic, la introducción de la impresión por inyección es emblemática de la cultura Mycronic. «Siempre hemos sido un poco desafiantes», afirma. «Cuando alguien nos dice que es imposible, eso nos empuja a pensar en grande. Esto se puede ver con nuestros generadores de patrones, así como con nuestras soluciones de ensamblaje. Hemos identificado oportunidades claras, por difíciles que puedan ser de resolver. Hemos hecho las grandes apuestas correctas. Y realmente han valido la pena para nuestros clientes».
Series más cortas, mayores ganancias
En la actualidad, Mycronic ha crecido junto con su base de clientes y ofrece soluciones para cada paso del proceso, desde la placa base hasta la PCB terminada, inspeccionada y revestida. Estas soluciones automatizadas de línea completa permiten a los productores más pequeños, a los fabricantes por contrato y a los equipos de producción internos iterar rápidamente nuevos productos y ofrecer un valor que no pueden lograr los fabricantes de gran volumen en el extranjero.
“No siempre estuvo claro que la automatización avanzada sería el camino a seguir para estos productores de alta flexibilidad”, dice Robert. “Hace unos 15 años, se suponía que todo se trasladaría a Asia. Pero para aquellos que se quedaron a pesar de los mayores costos laborales, nos hemos mantenido con ellos y nos hemos convertido en una extensión de sus negocios. Hemos sido excelentes a la hora de apoyar a estos clientes y mantenerlos rentables con la producción en series cortas”.
Ensamblaje basado en datos
Si hace veinte años el hardware era un gran obstáculo para los cambios rápidos de trabajo, hoy en día suele ser el software. Por eso, en los últimos años, Mycronic se ha centrado en simplificar todo, desde la creación y el ajuste de programas hasta la revisión de inspecciones. Con la ayuda de sistemas avanzados de aprendizaje automático y aprendizaje profundo, los fabricantes ahora pueden automatizar una variedad de tareas repetitivas de programación y ajuste.
Hola, esto es un comentario.
Para empezar a moderar, editar y borrar comentarios, por favor, visita en el escritorio la pantalla de comentarios.
Los avatares de los comentaristas provienen de Gravatar.